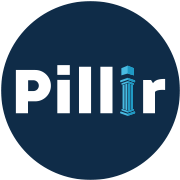
—
As a rapid, effective, and Edge-ready software development platform, Pillir reminds SAP Extended Warehouse Management (EWM) customers to look beyond the deployment model included in their basic licence.
Extended Warehouse Management (EWM), part of SAP AG’s SCM Suite, is SAP’s integrated system that addresses the challenges associated with complicated warehouse processes. It helps businesses handle a high volume of products by bringing agility to warehouse operations through digitization.
To help clients pick the most suitable SAP EWM deployment strategy, Pillir breaks down the differences between the two available deployment options: embedded and decentralised.
Pillir explains that Embedded EWM, a default offering in SAP S4/HANA 1610 release, now comes in two options: Basic Embedded EWM (included in the licence cost of SAP S4/HANA) and Advanced Embedded EWM. Besides replacing the SP WM (scheduled to phase out in 2025), the basic version offers top-notch functionalities for small to mid-sized customers. For more advanced optimization and automation, like yard and wave management, slotting, employee management, and billing, enterprises can pay more for the Advanced option.
On the flip side, decentralised EWM has been in action since the SAP S/4HANA 1511 release. In this deployment choice, the SAP EWM resides on its own server, has its own database, and gets connected to SAP S/4 HANA via CIF (Core Interface) and RFC (Remote Function calls).
Even though both decentralised and embedded deployment options enable supply chain businesses to make the most of SAP document types, transactional data, and master data, there are differences between them:
— While Embedded EWM can connect to a single SAP S4/HANA or ERP storage location, the decentralised option supports integration with multiple SAP ERP systems at a single or multiple locations.
— The Embedded EWM is not suitable for multiple warehouses or massive Material Flow System traffic, which is something that decentralised deployment can efficiently manage, along with a high level of automation that won’t impact the performance of other processes.
While seasonal demand peaks in transactions and improved warehouse throughput hint toward deploying a decentralised EWM system, it comes with a cost. Enterprises running their operations on Embedded EWM benefit from a lowered cost of ownership and ease of deployment, as they have only a single physical system to maintain.
Unlike the Embedded EWM, decentralised deployment can keep the warehouse processes running optimally in case the SAP ERP goes down. Additionally, while both EWM and ERP systems get upgraded without impacting each other in the decentralised strategy, enterprises that deploy Embedded EWM must ensure that their current IT infrastructure is sophisticated enough to handle the system upgrades.
The company emphasises that CIOs and warehouse managers should consider the upsides and downsides of both deployment strategies and select the one that best fits their company specifications, such as the level and type of operation optimisation and automation required. It is also critical to consider the complexity of the business structure when deciding the EWM deployment approach.
That said, the biggest downside of SAP EWM is that it lacks mobility. With an SAP EWM system in action, warehouse managers cannot get real-time insights into inventory and processes, and workers cannot input warehouse data at the point of tasks using their smartphones.
Pillir stresses the importance of utilising a platform that can offer seamless integration with SAP while ensuring the digital core is clean.
The company claims that its LC/NC platform’s out-of-the-box templates allow enterprises to build custom warehouse management apps in no time. The apps can be deployed in a few hours or days and can be seamlessly integrated with SAP ECC or S/4HANA environments for more streamlined and automated SAP-focused warehouse management operations.
Pillir adds that its platform’s offline capabilities allow warehouse workers to continue using the app without an internet connection, and will automatically synchronise their data as soon as the connection is restored.
In a recent testimonial, a Pillir customer writes, “We digitised and streamlined door management and loading/unloading activities – tracking of all these in our SAP system in real time instead of intermittently when someone had a chance to get to the terminal. This has helped us improve productivity in the warehouse significantly as well as real time visibility for our core business stakeholders in HQ.”
Learn more about Pillir by visiting https://www.pillir.io.
Contact Info:
Name: Tyler Young
Email: Send Email
Organization: Pillir
Address: 3133 West Frye Road, Chandler, Arizona 85226, United States
Phone: +1-855-277-7373
Website: https://www.pillir.io
Source: PressCable
Release ID: 89080787
If you detect any issues, problems, or errors in this press release content, kindly contact error@releasecontact.com to notify us. We will respond and rectify the situation in the next 8 hours.